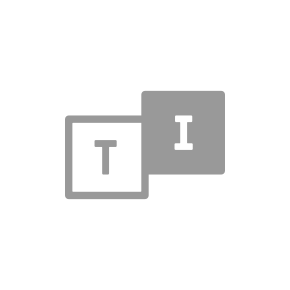
Druckwelle - ingenieur.de-Podcast zur Additiven Fertigung
Technology Podcasts
Ohne dritte Dimension ist alles flach. Additive Fertigung ist der Trend in der Produktion und Industrie. Bei Druckwelle holen wir führende Köpfe der Additiven Fertigung vors Mikrofon, die Ihnen 3D-Druck plastisch erklären. Die Experten erläutern neue Drucktechnologien und Materialien. Sie bewerten Entwicklungen und geben Praxis-Tipps. VDI-nachrichten-Redakteur Stefan Asche beschäftigt sich seit Jahren mit der Trend-Technologie. Als Ihr Host präsentiert er immer donnerstags, alle 14 Tage, eine neue Folge Druckwelle.
Location:
United States
Description:
Ohne dritte Dimension ist alles flach. Additive Fertigung ist der Trend in der Produktion und Industrie. Bei Druckwelle holen wir führende Köpfe der Additiven Fertigung vors Mikrofon, die Ihnen 3D-Druck plastisch erklären. Die Experten erläutern neue Drucktechnologien und Materialien. Sie bewerten Entwicklungen und geben Praxis-Tipps. VDI-nachrichten-Redakteur Stefan Asche beschäftigt sich seit Jahren mit der Trend-Technologie. Als Ihr Host präsentiert er immer donnerstags, alle 14 Tage, eine neue Folge Druckwelle.
Language:
German
Folge 83 - Häuser schneller und billiger 3D-drucken
Duration:00:33:50
Folge 82 - Vergangenheit und Zukunft des 3D-Drucks
Duration:00:59:13
Folge 81 - 3D-Druck, ganz nahe am Patienten
Duration:00:30:32
Folge 80 - Das Messer fest im gedruckten Griff
Duration:00:43:48
Folge 79 - DMRC Paderborn: Wo sich Wissenschaft und Praxis treffen
Duration:00:52:38
Folge 78 - Reparieren im Pulverbett
Duration:00:38:12
Folge 77 - Roboter trägt auf und fräst ab
Duration:00:28:42
Folge 76 - 3D-Druck für Bastler, für alle!
Duration:00:33:08
Folge 75 - Funktionale Kunststoffteile – mehrfarbig und hochpräzise
Duration:00:21:17
Folge 74 - Voll auf Draht – mit dem Laser
Duration:00:26:13
Folge 73 - Sensoren in Bauteile eindrucken
Duration:00:37:51
Folge 72 - Fertige Mikrooptiken in Serie gedruckt
Duration:00:18:43
Folge 71 - Bauteile aus Faserverbund – ganz ohne Form!
Duration:00:49:35
Folge 70 - Schnell und günstig zu besseren Spritzgießformen
Duration:00:44:44
Folge 69 - Feine Schokolade in filigranen Formen
Duration:00:26:38
Folge 68 - „Makro-SLM“: Metallteile aus einem gigantischen Pulverbett
Duration:00:25:19
Folge 67 - Saubere Autos dank 3D-Druck
Duration:00:58:32
Folge 66 - Eos: Mehr Nachhaltigkeit durch neue Materialien und Technologien
Duration:00:32:50
Folge 65 - Glas drucken, ohne zu sintern
Duration:00:18:48
Folge 64 - Ahoi, Herr KaLeu! – 3D-Druck bei Bundeswehr und Marine
Duration:00:33:17